
Thermal Barrier Coatings
Thermal barrier coatings play a crucial role in insulating high-pressure turbine blades within jet engines, allowing them to operate at higher temperatures for improved efficiency. These coatings, created through the process of Electron Beam-Physical Vapor Deposition (EB-PVD), exhibit a distinctive feathery columnar microstructure. However, the current coating material, 7YSZ (7% yttria-stabilized zirconia), has limitations in terms of temperature resistance and resistance to calcium-magnesium-aluminium-silicon oxide systems (CMAS). Consequently, there is a need to develop new thermal barrier coatings that meet specific requirements. These requirements include low thermal conductivity, high thermal expansion coefficient, high melting point, phase stability across temperatures, low sintering rate of the porous microstructure, and improved CMAS resistance. This was a group project as part of my MSc. Due to NDA, I have limited the details on the page.

CMAS Attack
During the operation of jet engines, inorganic particles known as CMAS (Calcia-magnesia-alumino-silicate) are ingested into the engine. CMAS deposits can melt and infiltrate the void spaces of the 7YSZ (7% yttria-stabilized zirconia) thermal barrier coating (TBC) due to high temperatures, leading to stiffness and strain tolerance loss. This can cause delamination cracks and progressive exfoliation of the TBC, reducing its insulation efficiency. Chemical interactions between CMAS and the thermally grown oxide (TGO) further contribute to TBC degradation. To combat CMAS attack, new TBC materials, such as Gadolinium Zirconate (GZO), have been investigated. GZO exhibits excellent CMAS resistance, reacts with CMAS to block infiltration, and offers lower thermal conductivity, higher sintering resistance, and higher melting point compared to 7YSZ.

Exploding Ingots
Electron Beam Physical Vapour Deposition (EB-PVD) is a method used to deposit Thermal Barrier Coatings (TBCs). In this process, the target material is heated and evaporated in high vacuum and directed towards the substrate. EB-PVD offers advantages such as high deposition rate, consistent results with low porosity, and controlled process parameters. However, GZO, which has improved CMAS resistance compared to 7YSZ, still has limitations in fracture toughness and erosion resistance.
​
Thermal shock-induced cracking of ceramic ingots during electron beam irradiation is a well-known phenomenon. Various research institutes and studies have encountered similar issues with different materials, including 7YSZ, YAG, Lanthanum Gadolinium Zirconate, Hafnia, GZO, and Alumina ingots. However, researchers have successfully addressed the problem by modifying the manufacturing process of the ceramic ingots. The literature suggests that adjusting and controlling critical properties of the ceramic during manufacturing can help mitigate thermal shock cracking.

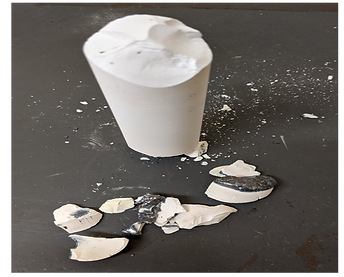
Material Characterization of Melted Ingots

Thermal Shock Mitigation Strategies
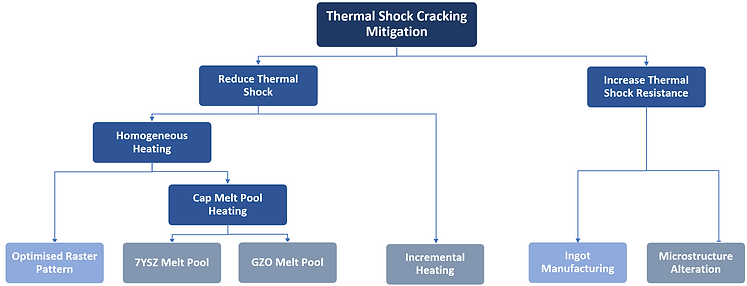
Experimentation
The cap melt pool method has been successfully employed to reduce thermal shock in ceramic ingot evaporation. Experiment 1 and Experiment 2 demonstrated the effectiveness of using a cap melt pool, either made of 7YSZ or a melted GZO ingot, for homogeneous and incremental heating. This method offers a faster alternative to traditional incremental heating procedures and has the potential to be applied to various ceramics. However, careful composition analysis is required to ensure complete evaporation and maintain the desired properties of the ceramic coatings.
Additionally, horizontal cracking observed in both GZO and 7YSZ ingots highlights the importance of controlling ingot manufacturing processes, such as sintering conditions, to prevent instability and explosions. Melted GZO ingots exhibit high thermal shock resistance due to factors like pre-sintering, thermal expansion accommodation, and the characteristics of the melted region, including its porosity, crystallization, and composition.
​
Due to time limitations, optimised Raster Pattern and Ingot Manufacturing were only explored theoritically. The incremental heating method has worked empirically but the time duration is impractical for industrial use.


Preferential Evaporation
The preferential evaporation of gadolinium observed in the GZO melt pool, compared to zirconium oxides, can be attributed to the difference in vapor pressures between gadolinium oxide and zirconium oxides. This results in incongruent or unstable evaporation initially, until a stable composition is reached. However, by depositing the coatings a few minutes after the initial evaporation, nearly stoichiometric gadolinium zirconate coatings can be achieved. This can be achieved by using a delayed introduction of parts or employing a shutter system. The duration of the unstable evaporation phase is estimated to be around 5 minutes for GZO. It should be noted that the preferential evaporation sets a limit on the combination of materials that can be evaporated from a single ingot, as composition fluctuations in the melt pool may lead to significant variations in the coating composition.
